In our fast-paced world of convenience foods and busy lifestyles, we often overlook micronutrients, which…
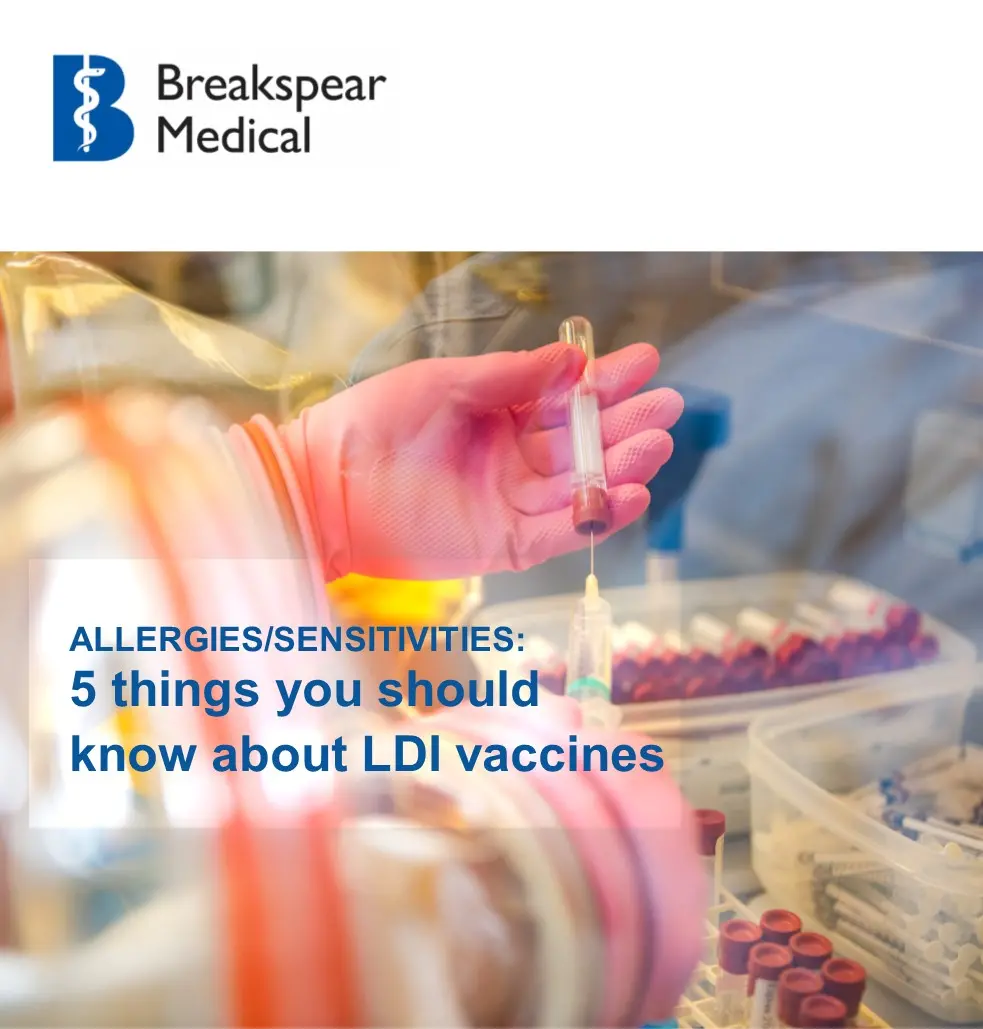
5 things you should know about low-dose immunotherapy vaccines
If you are a patient at Breakspear Medical with allergies/sensitivities, chances are you are currently taking low-dose immunotherapy (LDI) vaccines or have heard about this method of allergy/sensitivity testing. In this blog, we share 5 interesting facts about our LDI allergy/sensitivity treatment programme.
Edited excerpt from Breakspear Medical Bulletin Issue 37:
Breakspear Medical specialises in the treatment of allergy, intolerance and sensitivity using the proven technique of allergen-specific low-dose immunotherapy (LDI).
Each patient who undergoes LDI testing will be prescribed their custom-made, preservative-free LDI vaccines.
Fact 1: all our LDI vaccines are manufactured on-site
Breakspear Medical’s Manufacturers’ “Specials” Licence laboratory is on the first floor of our main building.
Every antigen vaccine is custom-made to fulfil each patient’s prescription and manufactured to the high standards demanded by the Medicines and Healthcare products Regulatory Agency (MHRA).
Each day, the laboratory staff are producing vaccines for patients on Breakspear Medical’s Testing Wards and for patients who have reordered their vaccines. They also produce vaccines for patients testing and reordering at other clinics.
Fact 2: our LDI vaccines are custom-made by people, not machines
Our Antigen Laboratory staff, Andrea, Helen, Sam and Marion, prepare, manufacture and dispatch all the LDI vaccines produced at Breakspear Medical.
Before entering the pressurised and air-filtered environment of the laboratory, the technicians must follow strict procedures of changing into their laboratory uniforms, including shoe covers and hairnets.
The cleanroom clothing is made from a special material that minimises the shedding of particles from the technician.
Each morning, the laboratory is cleaned and monitored by the laboratory technicians before any production can begin.
During production, the technicians are each seated at an individual small laboratory cabinet, with their arms reaching in through extra-large long rubber gloves to work with the small volumes of liquids, syringes and vaccutainers to create each cocktail.
Fact 3: LDI vaccines cannot be made in less than 28 minutes
From start to finish, with no interruptions or supply issues, 1 antigen vaccine cocktail (a tube of up to 25 different antigen items) can take approximately 30 to 40 minutes to manufacture. Technicians are working on cocktails, as well as fulfilling various other responsibilities and adhering to strict good manufacturing practice (GMP) and environmental validation conditions, and every vaccine is tested for sterility.
Sometimes there are delays in production because the items required for one cocktail may be being used by another technician for another patient’s cocktail. Sometimes the patient requires changes to endpoints partway through production, which means that the order may have to be re-started. And, of course, being people, occasionally the technicians need personal breaks and must take scheduled lunch breaks, which requires them to change from their laboratory clothes, exit the cleanroom and then upon returning to work, go through the sanitising laboratory entry process again.
The laboratory must keep to a strict time schedule for the start of manufacturing and shut down at the end of the day. Shutting down at the end of the day requires sanitising and maintenance work before the staff’s shifts end. This means that once the shutdown procedures are underway, it is not possible for the technicians to continue with any more production for the day.
Fact 4: we offer over 520 standard antigens, including foods, pollen and supplements
Our laboratory supplies the Breakspear Medical testing ward with 522 antigen vaccines to enable the nurses to test patients 5 days per week.
Each vial of antigen vaccines has an expiry date 3 months from manufacture. This means that the laboratory must constantly monitor and replenish stock levels and manufacture entire new runs of all the testing vaccines every 3 months. Thus the laboratory has to prepare 3400 individually labelled tubes when renewing the testing wards’ supplies, in addition to manufacturing the daily patients’ individual prescriptions.
Fact 5: we can create unique testing and treatment antigen vaccines
All base ingredients for the antigen vaccines are sourced by the laboratory staff and the antigen vaccines are produced entirely on-site.
If we do not have a food or inhalant or other item for which a patient requires an antigen vaccine, our laboratory can manufacture one for an additional charge.
To create a unique antigen vaccine, a sample of the substance needs to be provided. For example, if a patient had an adverse reaction to a rare food, such as dandelion leaves, the laboratory would require a 2 gram sample of the food to produce the testing and treatment vaccines.
The food sample then goes through the same processing techniques as standard vaccines, which include processing in a saline solution and being filtered and sterilised.
Creation of a non-standard vaccine does take additional time and the unique antigen solution requires additional storage space in the special laboratory freezers, which is why there is an extra charge for this service.
Breakspear Medical is proud
Breakspear Medical is proud to have maintained the high MHRA standards in our laboratory since 1993. For over 30 years, the laboratory team has produced thousands of antigen vaccines and has an exceptional success record of delivering the customised vaccines within 14 days of orders being placed.